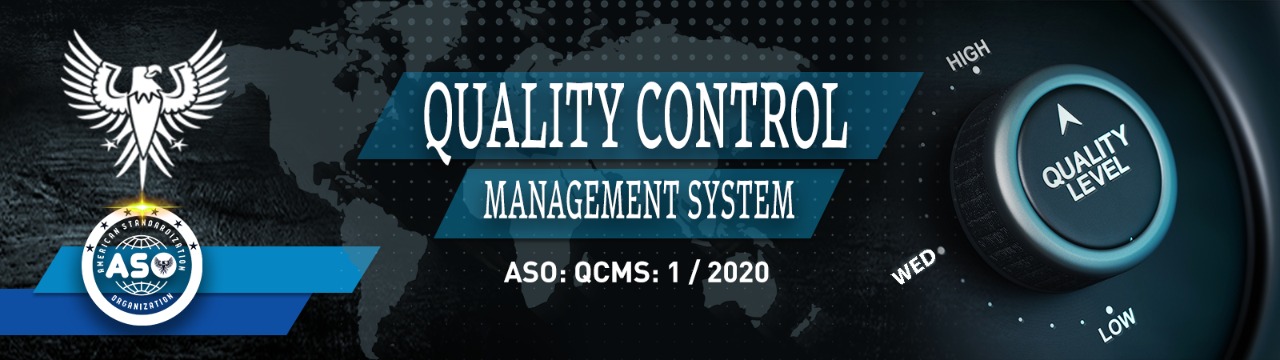
The standard for Quality Control Management System
By
Technical Committee for Quality Control
The Technical Committee for Quality Control of the American Standardization Organization has established this standard aiming to ensure providing perfect services and flawless products which conform to the specifications and standards previously set by clients.
Introduction
American Standardization Organization, Inc. was formed under No. 3951733 issued by the American specialized governmental authorities in the State of Delaware as a private non-profit organization whose main purpose is to set the various administrative and technical standards to boost the requirements and ambitions of the clients.
These standards have been set for the corporations that seek the clients` satisfaction and meeting their requirements by presenting a flawless product and perfect services. QCMS focuses on the essential requirements, specifications, and standards and required resources for the implementation of service or the product properly and accurately, aiming to meet the client`s requirements. This standard consists of three principles and three processes.
Principles:
Customer requirements – Customer participation – Customer Complaint.
Processes:
Planning – Implementation – Analysis
Principles of QCMS
First Principle: Client Requirements
The focus shall be on the customer`s requirements accurately to guarantee his satisfaction through quality control of products and services he obtains. These requirements could be specifications, standards, and specific terms mentioned in the contract or others. Therefore, they shall be kept in a suitable safe place.
Second Principle: Customer participation
The client shall participate in the process at all times to guarantee to get all the strength and weakness points, and opportunities for improvement set by the client himself for the service or the product he gets.
The more the corporation works on the client`s participation and expressing opinions regarding the service or the product provided by the corporation, the more he trusts in the service or the product presented.
Since the client is not easy to satisfy, new ideas and methods are required for client participation to get the client`s trust in the service as much as possible.
Third Principle: Customer Complaint
Customer complaints shall be identified and analyzed to abstract the main reason for the complaint to follow what is necessary to satisfy the client, and the management shall work hard to avoid such complaints later.
Note: If the client does not feel the credibility of the corporate management and their interaction with the complaint to obtain the client`s satisfaction, by all means, that could be a bad sign of losing the client`s trust in the product or the service provided.
Standards for Quality Control Management System
ASO: QCMS: 1 / 2020
-
Scope:
This standard is concerned with the basic quality control management system standards in planning, implementing, and analyzing the stages of the product or service provided to clients that can be applied in all fields and activities of all establishments, whether productive or service in general. Any establishment that is legally licensed by competent government authorities to practice its activity has the right to obtain a certificate of accreditation. All requirements that follow are mandatory for the establishment that seeks to obtain accreditation.
-
System:
Documents and resources needed to meet the client’s requirements.
-
Administration:
Planning, implementation, and analysis.
-
Control:
Assurance of meeting the client’s requirements.
-
Quality:
Meeting the client`s requirements.
-
Planning:
Defining future goals.
-
Implementation:
Activation, control, and analysis of plans and objectives.
-
Quality Controller:
The person responsible for planning, implementing, analyzing, preserving, and documenting the system, examining and testing services or products, and verifying they fulfill the client`s requirements, and he has all the powers
-
Quality Control Documents:
Specifications, standards, plans, objectives, samples, and records used in the quality control process. -
Data Analysis:
To measure the performance of what has been implemented with what has been previously planned to find out the causes of any differences from the planned implementation to reduce or eliminate them, and to know the strengths and weaknesses. -
Quality Assurance:
Assurance of the extent to which a product or service conforms to the specifications and standards previously set. -
Quality Control:
Measuring the actual quality and comparing it with the required specifications, and following the necessary process to adjust those different ones. -
Conforming Product or Service:
The product or service meets the specifications and standards that have been previously set. -
Non-conforming Product or service:
The product or service does not meet the standards and specifications that have been previously set. -
Control of a product or service:
Identification and control of a conforming or non-conforming product. -
Specifications and standards:
A set of rules that regulate the activity of the quality control management system QCMS for the benefit of all concerned parties.
Note: – The quality controller must keep a facsimile copy of the pre-defined specifications and standards so that he can take the charge of inspection and testing process accordingly. This copy must be kept safe away from damage or loss and to be easily retrieved. A copy shall be kept with the top management.
Note- The specification and standards can be required by a government, a client, or specific standards of an establishment or other. -
Standardization of measuring tools used in examination and inspection:
The measuring tools used for testing and inspection shall be calibrated. This item can be excluded for establishments that do not use measuring tools that require standardization.
A catalog of the measuring tool that has been used for inspection and testing can be used to determine whether or not it requires calibration. The board of the establishment must provide physical evidence to show the intention of implementing the calibration of the used measuring tools.
-
Basic Phases of Quality Control:
Pre-production or service Phase:- Imports testing.
Production or service Phase: – Testing stages of service or product.
Final Phase: – Testing the final service or product.
The facility management must identify, plan, implement, and analyze the necessary quality control phases to takeover all stages of the product or service to avoid providing any defective services or products to customers.
-
Testing and Inspection:
Assurance of the extent to which a product or service conforms to the specifications and standards that have been set. -
Customer Survey (Client Participation):
To get the client’s opinion and to what extent he is satisfied with the products he obtained to identify the strengths and weaknesses and the chances of improvement for the provided products or service.
The survey shall include the customer opinion about the quality of the products or service, how suitable is the price, and the duration for obtaining the products or service.
-
Customer Complaint:
It is the client`s dissatisfaction with the product or service provided; which can also be an opportunity for improvement and avoiding errors.
The complaint shall be accurately defined and described, identifying the main cause of the complaint, and the appropriate corrective action taken to avoid repeating the same complaint.
The complainant customer shall be satisfied whenever possible.
Complaints, especially recurring ones, shall be limited and presented to the top management to take appropriate corrective actions.
-
Top Management:
It`s responsible for providing all the requirements of the quality control management system and taking the necessary actions regarding customer opinions and complaints to keep their existence, and documenting the necessary decisions and recommendations that work on reducing problems, complaints, and defective rates of services or products in cooperation with the quality controller.
Table of required documents to be created, implemented and maintained in the QCMS:
Required Documents |
|
1 |
Government license for the facility to conduct its activities |
2 |
Accreditation request |
3 |
Decision to appoint a quality controller |
4 |
QC inspector Job Description Card |
5 |
QC plan |
6 |
Examination report |
7 |
Control of non-conforming product |
8 |
Calibration of testing and inspection equipment |
9 |
Customer opinion survey |
10 |
Client complaint |
11 |
Decisions and recommendations of top management |
12 |
Data analysis and performance measurement |
13 |
Phases of production or service process in the facility with defining testing and inspection points |